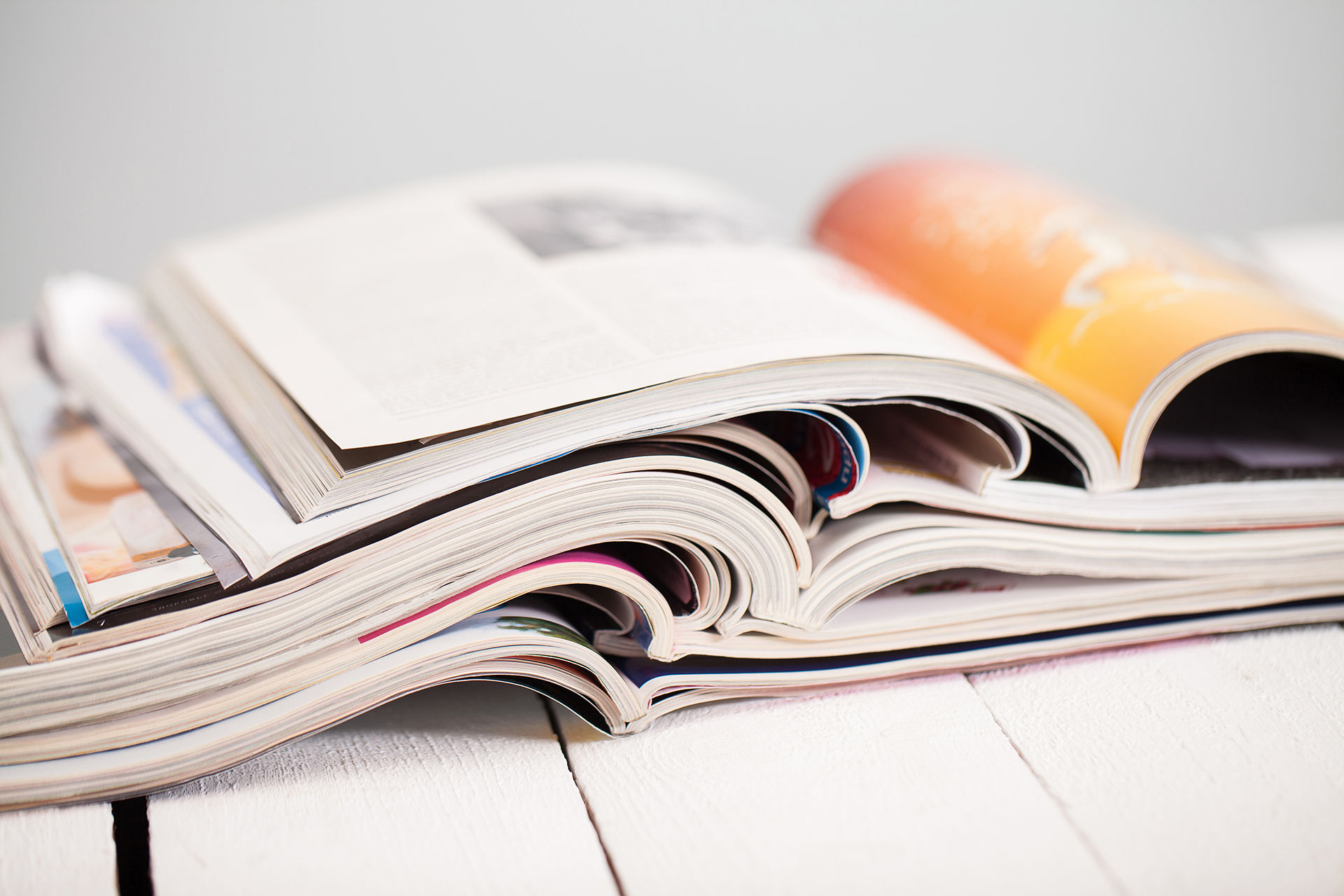
Dip Molding
Quick Glance
Unit Cost
Surface Finish​
Tolerance
Cost of capital investment
Production volumes
Possible geometries
A mold is produced then dipped into a hot or otherwise liquid plastic, ool, and then removed from the mold.

Process:
One of the more simpler processes to grasp, it involves dipping a mold into a liquid polymer bath and then peeling it off from the mold. The molds are typically heated to a similar temperature as the polymer liquid before dipping to ensure consistent curing. Then the mold is brought over to the liquid bath and dipped to coat the mold. A number of factors influence the wall thickness including mold temperature, the temperature of the material, the speed of dipping the mold, duration of the dip, and speed the mold is removed from the plastic bath.

Controlling wall thickness is one of the more difficult aspects of this process due to the number of influencing factors. Experienced manufacturers should be able to control the thickness with a fair amount of consistency but still might take a number of iterations to finalize the process for a new part. Items such as latex gloves have been manufactured to such a scale that features such as thickness and texture have been well established with a high level of consistency. In some highly controlled productions, the wrist of the gloves has a larger wall thickness than the fingers to give the gloves extra strength when applied while still maintaining sensitivity at the fingers.
After the dipping process, the parts move onto an additional oven cure the liquid into a solid. The parts are then moved to a liquid bath or spray to cool the parts to prepare them for the final removal from the mold. Parts are then dried off and ready for packaging.
Applicable Materials:
Limited to softer and flexible materials such as PVC, Latex, Polyurethanes, Elastomers, Silicones, Plastisol
Advantages:
Suitable for high or low production volumes
Tooling is generally very affordable compared to other tooling for plastics
Unit cost is also highly economical
Disadvantages:
Limited to more basic geometries
Hard to control for uniform wall thicknesses and difficult to added controlled variance
Cycle times are fairly long it often required large numbers of molds to be produced for production
Example Products:
Balloons, Condoms, Gloves


Looking to learn more or have a project that needs Dip Molding?